An Innovative Trenchless Solution Saves a Colorado District Time and Money
When a robotic inspection confirmed that the 1.5-mile-long Colsman Tunnel showed signs of serious deterioration, the Southgate Water and Sanitation District knew it had a major capital improvement project on its hands. The tunnel,
which conveys 100 percent of the district’s 12.4-MGD sanitary peak flow under the community of Centennial, Colorado, would require either a major repair or a complete replacement.
The most conservative, proven approach would be to bore a new tunnel and create a redundant parallel system. This approach would likely cost more than $30 million and take two to three years to complete.
A Creative Use of Available Technology
Our Denver office is fortunate to have a strong, trusted partnership with Garney Construction, a national firm that has been in business nearly as long as Dewberry. Our firms have completed numerous challenging projects in the water and wastewater
industry together, including design-build delivery projects. When Southgate turned to our team to assess the alternatives for the Colsman Tunnel, we considered several approaches, including the conventional option of building a new and expensive tunnel.
Another option stood out, however, as an approach that would save the district a significant amount of time and money: a trenchless solution involving sliplining the tunnel with a new pipeline. Our design-build team ultimately recommended the slipline
option with a 48-inch high-density polyethylene (HDPE) pipe using a horizontal directional drilling (HDD) system, but there was a risk: the HDD slipline approach had rarely been used for water and wastewater projects, and never for a tunnel of this
length.
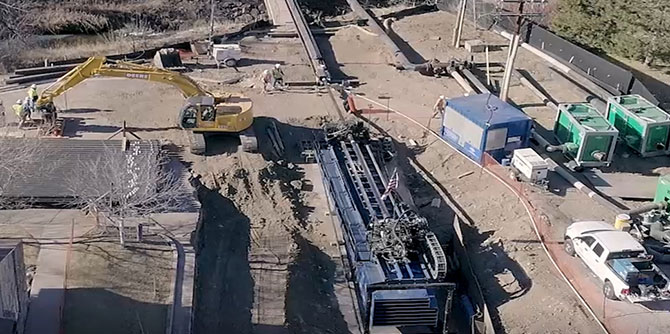
Teamwork: Addressing Challenges Together
The sliplining project was a first for me. I had recently joined the Denver office after working for several years on the East Coast. The Colsman Tunnel project became my first assignment at Dewberry. From the very beginning, it was clear what would
make this project a success: teamwork. That included ongoing collaboration within Dewberry, where I could easily reach out to many knowledgeable engineers for guidance, as well as with the team at Garney Construction. We worked closely together, day
in and day out, with open communications and a cooperative, can-do spirit. The fact that this was a breakthrough project—there were no similar projects elsewhere for us to reference—didn’t hold us back.
Construction took just six months. The fused HDPE pipe was fed into the tunnel at the western portal, with a machine set up at the eastern portal for the pull-in. Grouting the annular space between the tunnels was a critical phase of the project,
involving a barometric loop to keep the pipeline full and mitigate thermal expansion and pipeline buoyancy. Garney oversaw the drilling of injection points over stretches of 600 feet, up to 90 feet underground, and verified the grout placement with
specially built cameras. Together, we addressed many other challenges, including determining the exact geometry of the existing tunnels without reliable records, and determining pipe loading/stresses with the long HDPE pipeline installed in a 1.5-mile-long
tunnel with no intermediate access in live flow.
Risk and Reward: The Colsman Tunnel Sets a New Standard
The risk and the effort paid off. With the final cost of $8 million, we were able to save Southgate millions of dollars. The much-compressed construction timeline minimized the impact on the community, including road closures. Our team has been
proud to be recognized nationally by Trenchless Technology magazine, and internally with the 2019 Chairman’s Award for Innovation. The Colsman Tunnel rehabilitation represents the right team and the right approach, with a high-value
result for our client.