Pharmaceutical companies produce high strength wastewater, presenting some unique needs and challenges. For one company in North Carolina, the amount of wastewater generated was going to significantly increase when they doubled the size of their production facility. We were hired to do a technology evaluation to provide a solution to the challenges that this increased wastewater flow would cause.
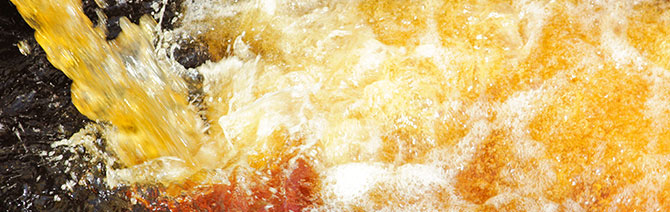
Jumping into the Trenches
To start, we worked closely with the operators to better understand how the existing 0.5-million gallon per day (MGD) wastewater treatment plant (WWTP) was operating. We identified infrastructure and operational optimization opportunities which would enabled the existing WWTP to operate more effectively.
We then estimated the WWTP's projected future load, and evaluated various technologies that would produce high quality effluent. Since onsite reuse is desired at the facility long-term, a membrane biological reactor (MBR)-reverse osmosis (RO) system emerged as the preferred alternative.
In this part of North Carolina, there have been a number of droughts, so this technology was especially important as a way for the client to secure available water.
Taking the Client to See a Full-Scale Installation
After outlining the advantages of the MBR-RO alternative, including footprint, effluent quality, and reuse savings to the client, we arranged a tour of a similar pharmaceutical production facility who had installed the MBR technology. The client was able to observe and discuss the technology with an owner who had experience it.
Bringing a Pilot-Scale Unit on Site
To test the MBR technology for the client, we teamed with General Electric (GE) to provide a pilot-scale unit at the client site. We operated the onsite pilot unit continuously for five months to evaluate system performance under varying conditions, and to allow for client observation. The pilot testing results exceeded expectations, producing reusable quality effluent even under high loading conditions.
Saving the Client Money
While onsite, we learned that the client generates a high strength spent polyethylene glycol (PEG) waste that is not treated at the onsite WWTP. Instead, it's collected and hauled off site for disposal—costing nearly $200,000. We suggested that the PEG waste may be amenable to biological treatment and recommended testing the treatability of the waste in the MBR pilot unit. Our testing confirmed that the PEG waste was treatable onsite, saving the client $200,000 per year in disposal costs.
Generating Drinking Quality Water
MBR pilot effluent was further treated by an RO membrane. The RO unit generated drinking quality water, allowing for significant reuse opportunities within the plant—in the cooling towers, boilers, or in the production process.
Reuse within production at a pharmaceutical facility can be challenging and requires additional treatment after the RO, as well as validation from the Federal Drug Administration. Until this project, effluent reuse in production is generally not observed in the United States pharmaceutical industry, but is more frequently observed in Puerto Rico and Europe.
Providing More for Our Clients
At the end of the pilot study, we were asked to perform additional design work for the next phase of the project. We designed an upgrade to their headworks system, which included two one-million gallon, stainless steel, above ground tanks with coarse bubble diffusion, blowers, mechanical screening, grit removal, and pH neutralization tanks.